The LSG series flat wire gauge and measurement control system uses a dual-laser detection head with auxiliary fixtures for non-contact, high-precision online or offline measurements. Its advanced edge detection technology excels in flat product detection, ensuring measurement accuracy and efficiency. The design fully accommodates diverse application needs. The integrated laser scanning system provides precise results without damaging the surface of the measured object, making it ideal for high-precision industrial applications.
Main applications include: width and thickness measurement of photovoltaic ribbons, metal flat wires, flat enameled wires, and surface particle defect detection.
Also applicable to the outer diameter, width, and thickness measurement, as well as surface defect detection, of various wires such as enameled round (flat) wires, copper wires, tungsten wires, and photovoltaic ribbons.
| High collimation light source |
| Edge detection optimization |
| Dual-axis sampling |
|
|
The high-precision, parallel, collimated, and equidistant optical imaging system accurately identifies the target edges of the measured object, ensuring linear measurement accuracy and precision at different positions within the testing area. |
|
Ensures precise identification of the target object's edges. |
|
High-speed dual-axis scanning, simultaneous detection of width and thickness. |
|
| 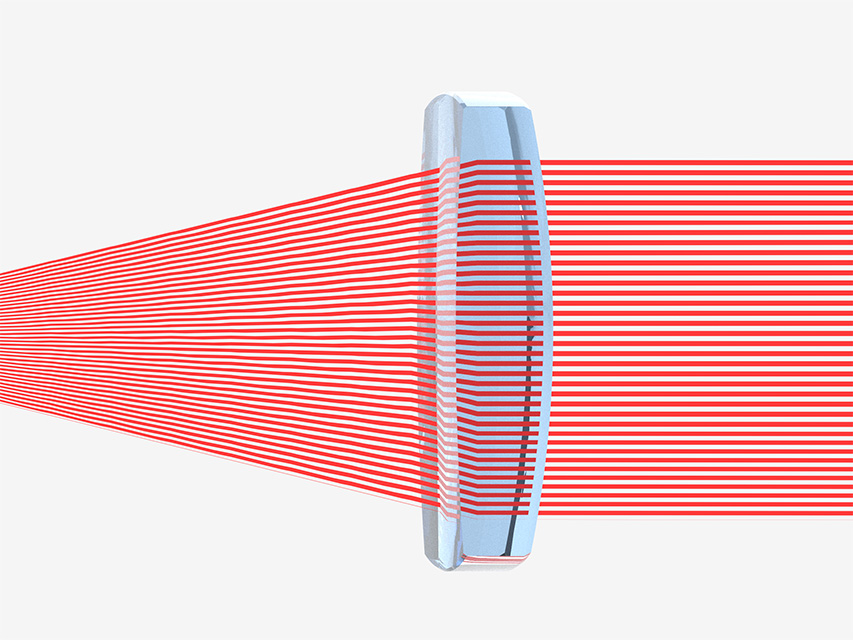
|
| 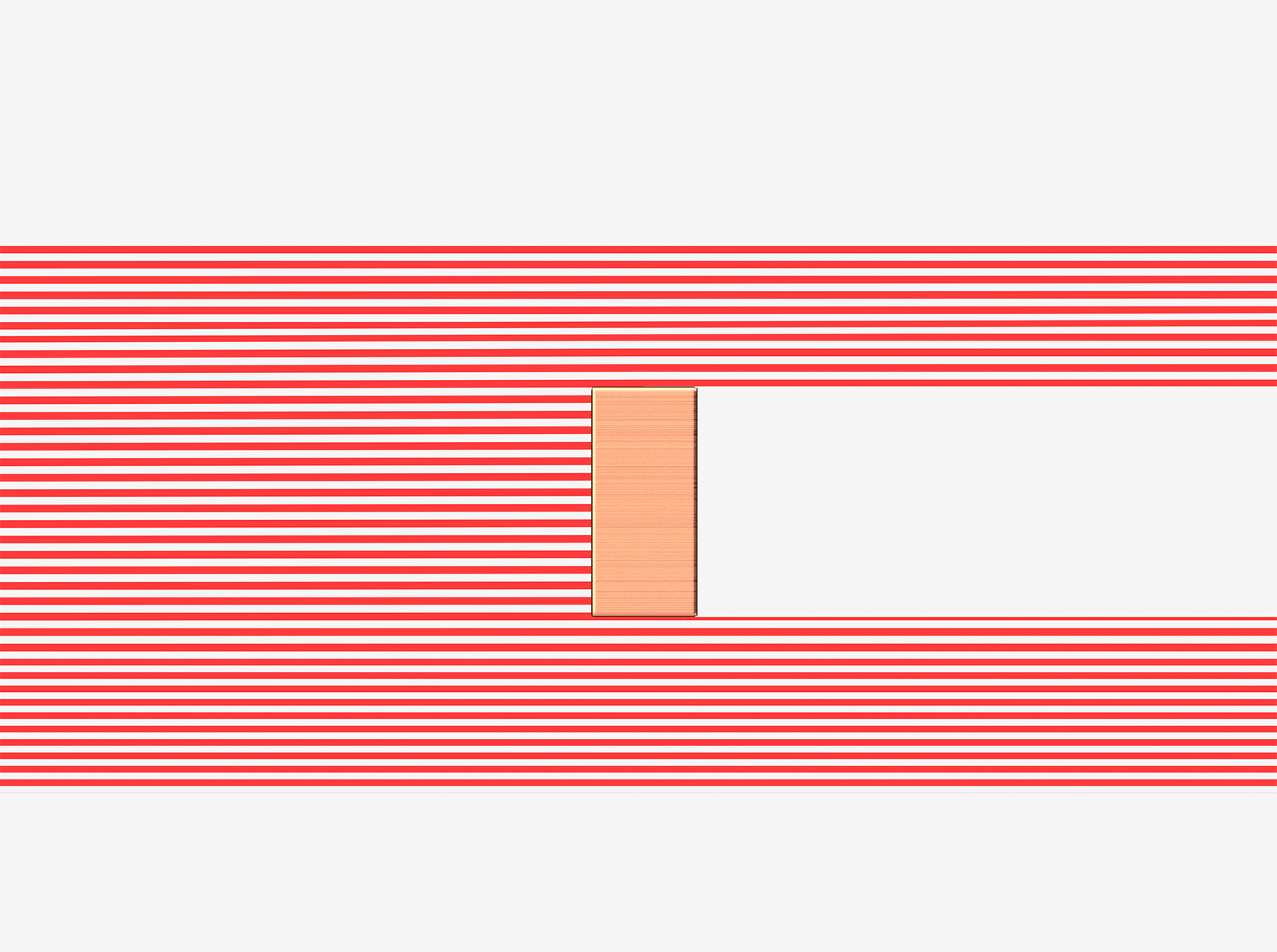
|
| 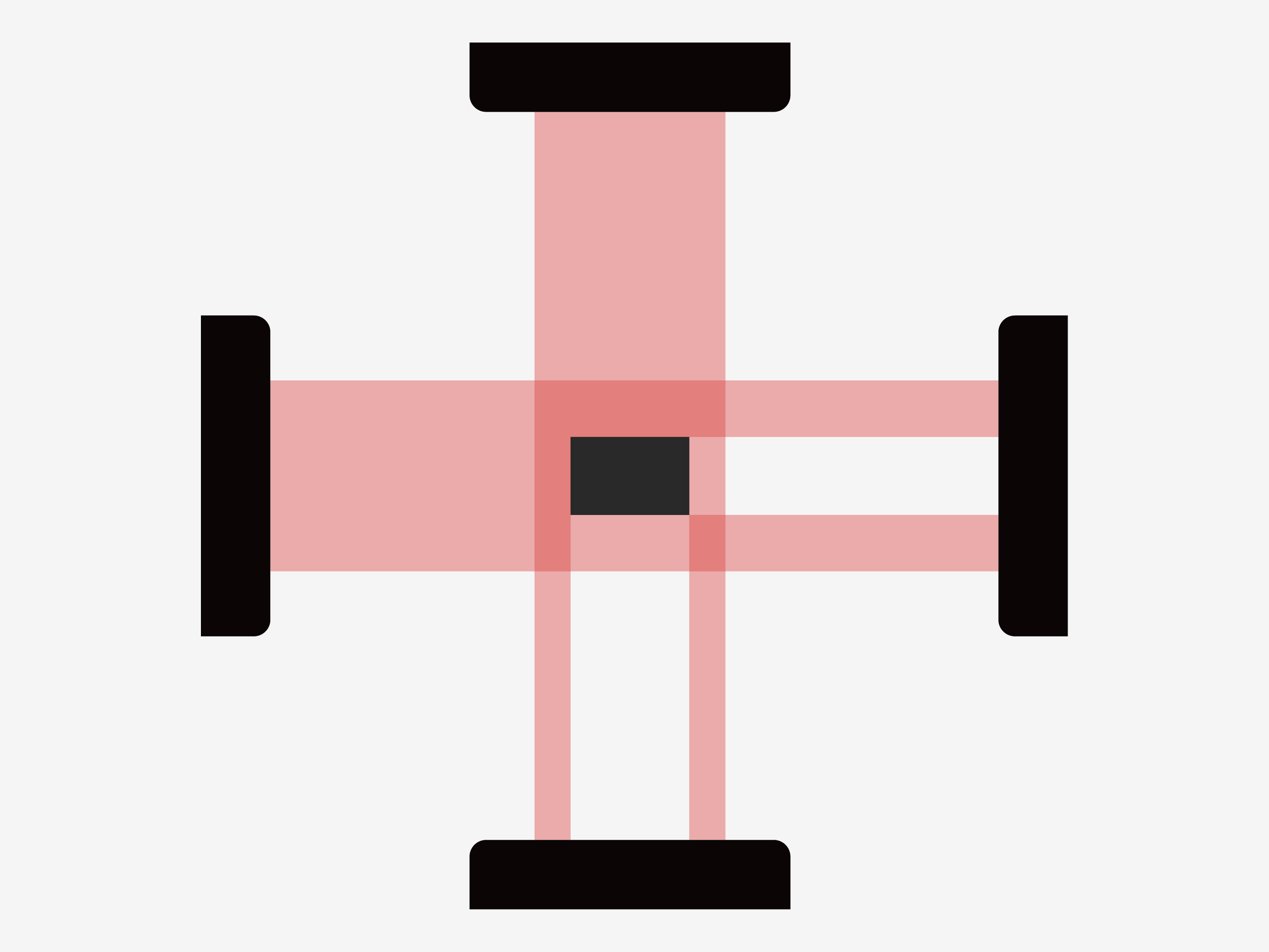
|
|
|
|
|
|
|
|
|
|
|
|
|
|
|
|
| DSP digital signal processing | | Online communication | | Long-term stable operation |
|
|
High-speed DSP technology processes large volumes of data in a short time, ensuring data integrity and accuracy. |
|
Standard communication protocol, secure, stable, and reliable. |
|
Customized optical transmission components and industrial-grade design ensure long-term operational stability. |
|
| 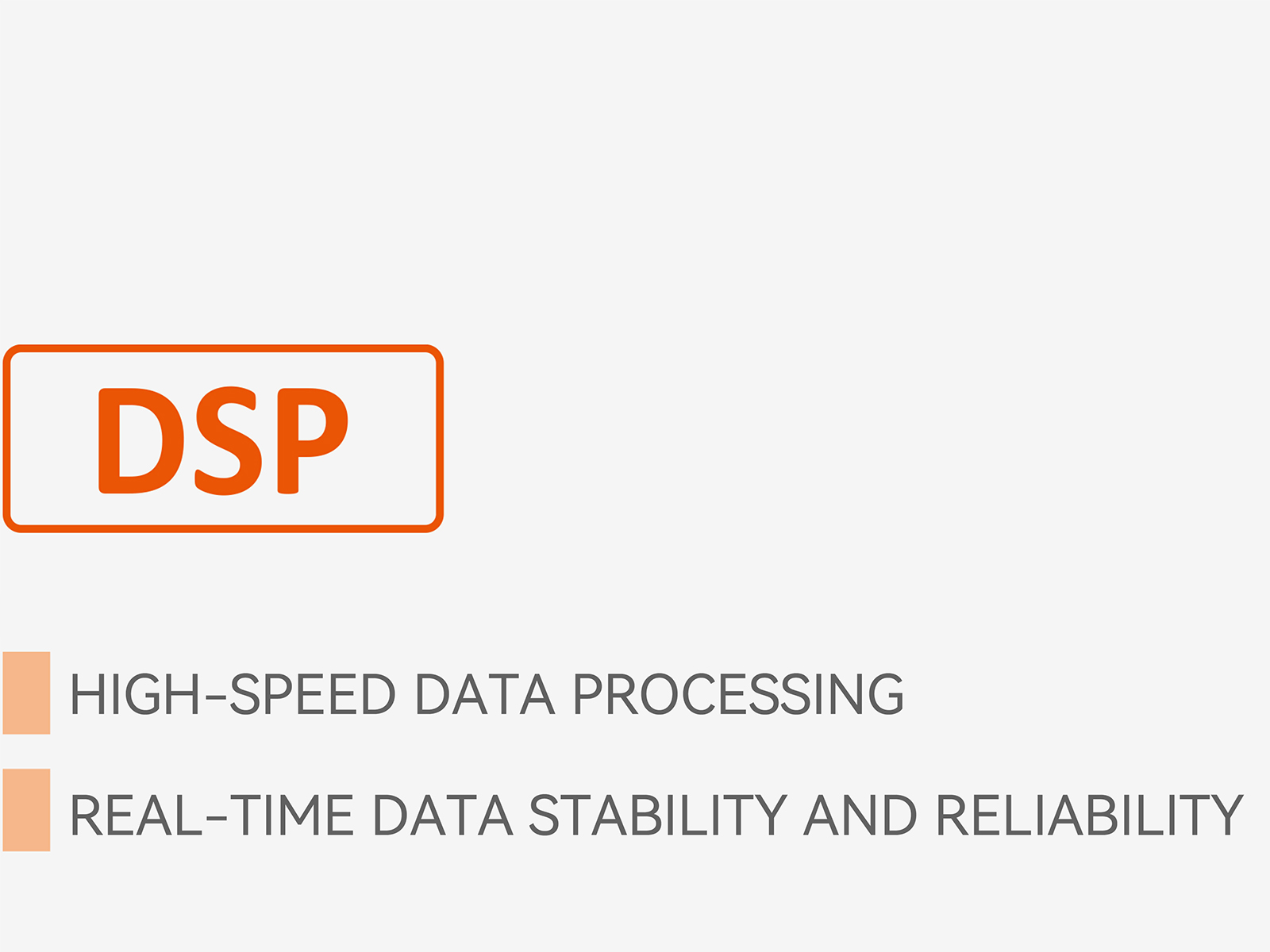
|
| 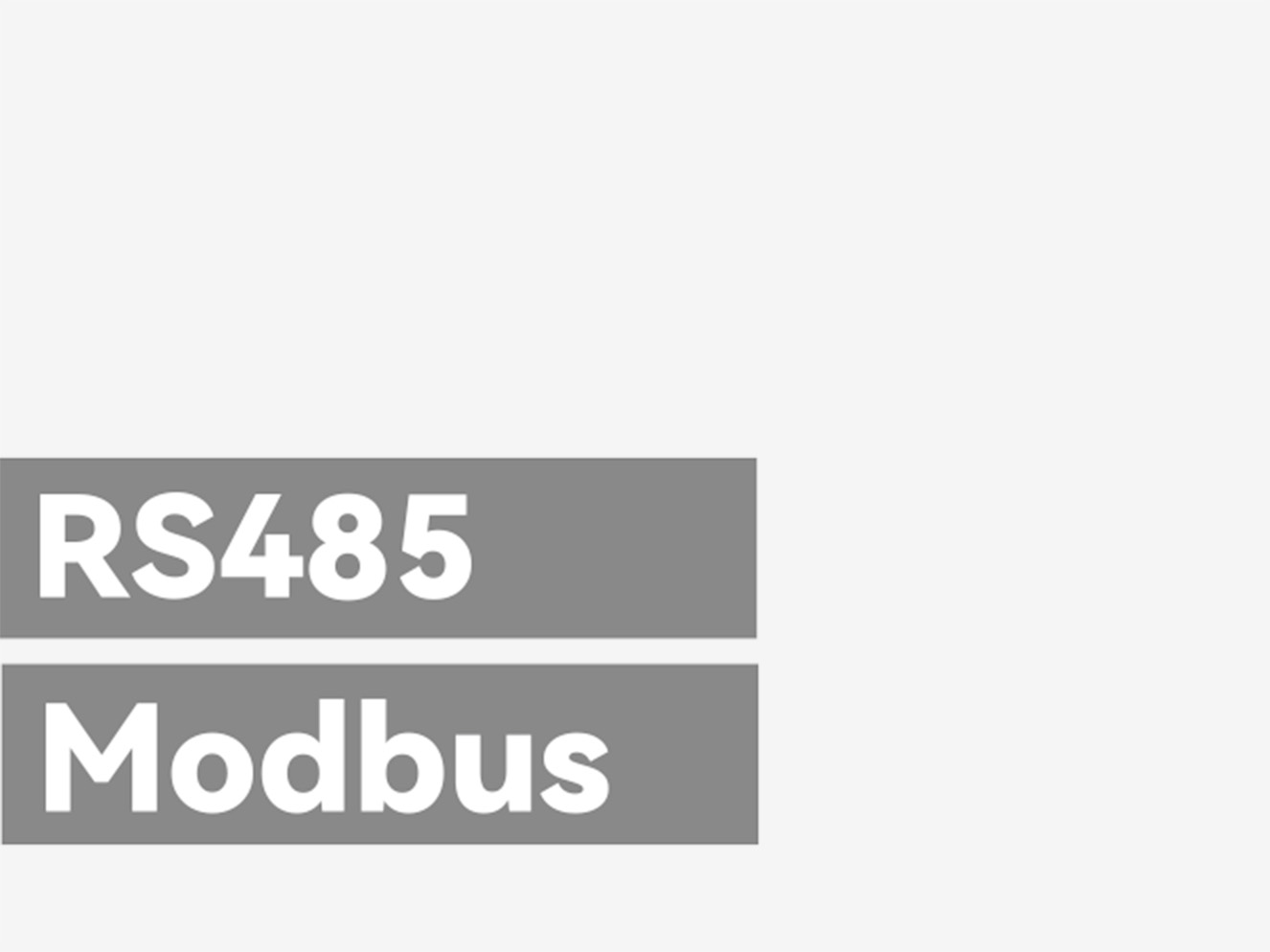
|
| 
|
|
|
|
|
|
|
|
|
Common surface defects of flat wires
| The flat wire diameter gauge, with customizable high-speed sampling frequency, provides an efficient and cost-effective solution for detecting surface defects in flat wire during online production. When defects such as bubbles formed during the varnishing process of flat enameled wires occur, the LSG-1020XYF gauge can accurately detect and record the bubble's position, triggering an alarm to ensure product quality and enhance production efficiency.
Additionally, through the software system, alarm signals can be triggered, and defect positions, sizes, and types (X direction: concave, convex; Y direction: concave, convex) can be recorded.
|
|
| 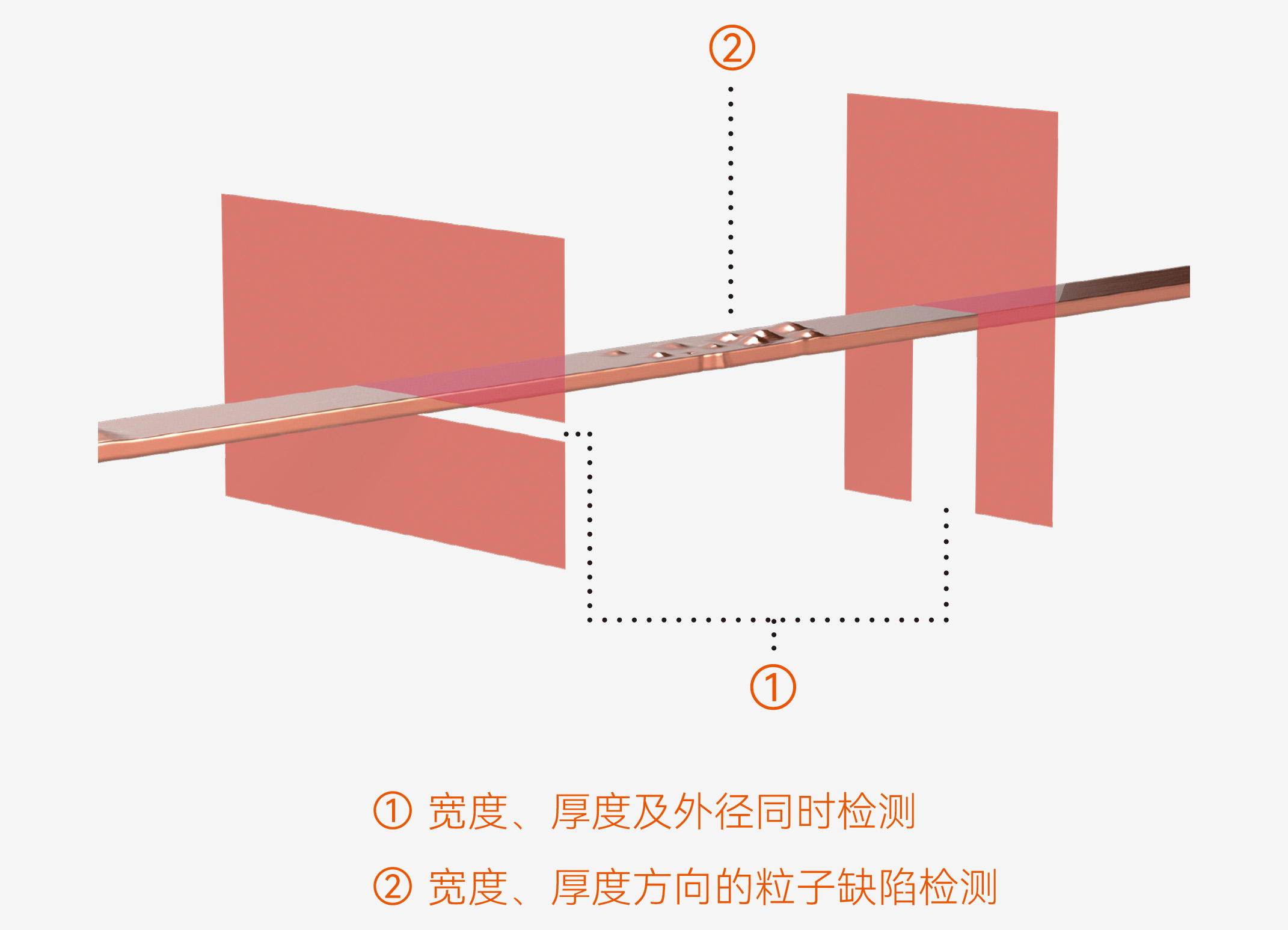
|
|
Intelligent Software System
|
|
|
|
|
| 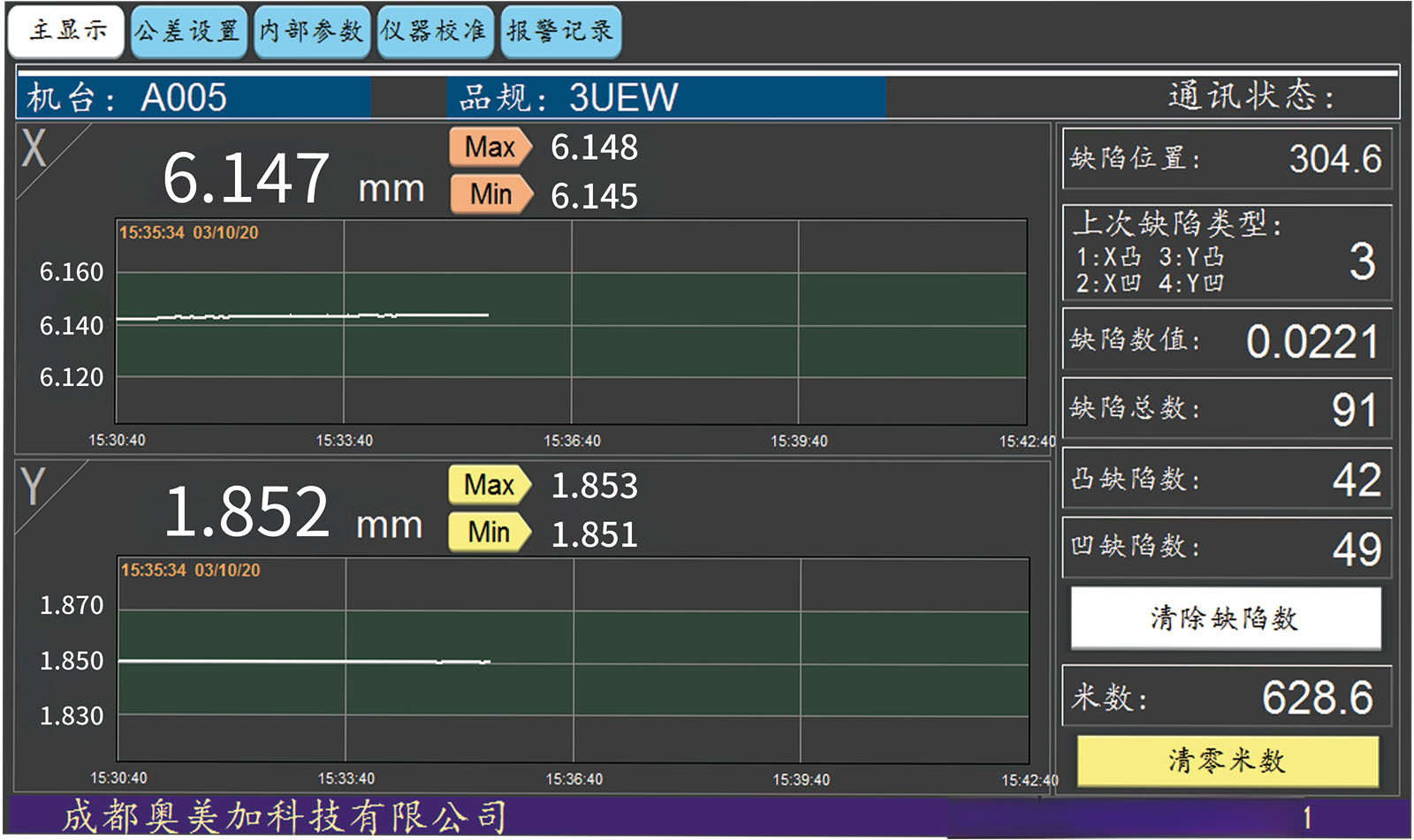
|
| 1.Real-time Data Display: Records and displays the outer diameter measurement values along with the variation curve, allowing for historical data retrieval.
2.Out-of-tolerance Alarm: Allows users to set tolerance parameters for outer diameter based on production processes. When measurements exceed the set limits, the system triggers an alarm and marks the deviation on the diameter curve.
3.Defect Detection and Positioning: Records the number of concave and convex defects, and marks defect locations based on preset speed, ensuring efficient monitoring and quality control. |
|